Flashpoint Recovery
Introducing HT FluidFit
Our ground-breaking flashpoint recovery service ensures the safe, compliant maintenance of flashpoints in your thermal fluid system without the need for an expensive drain and refill.
Overview
HT FluidFit is a revolutionary, proactive service for the maintenance and safety of thermal fluids; it offers a real alternative to the costly and time-consuming process of fluid disposal and re-filling of systems. Using state-of-the-art fluid conditioning rigs, fluids are maintained at their optimum condition with the potential to extend fluid life by a factor of 10 or more.
Processes remain up and running and the expense of purchasing new oil is avoided. The rigs work by reconditioning the existing oil via the systematic inline removal of volatile organic compounds (VOCs), returning the oil to a safe condition. Based on the innovative ‘flash evaporation’ technology developed with patented technology from many years of engineering, the rigs are an ideal way to keep your process safe and cost-effective.
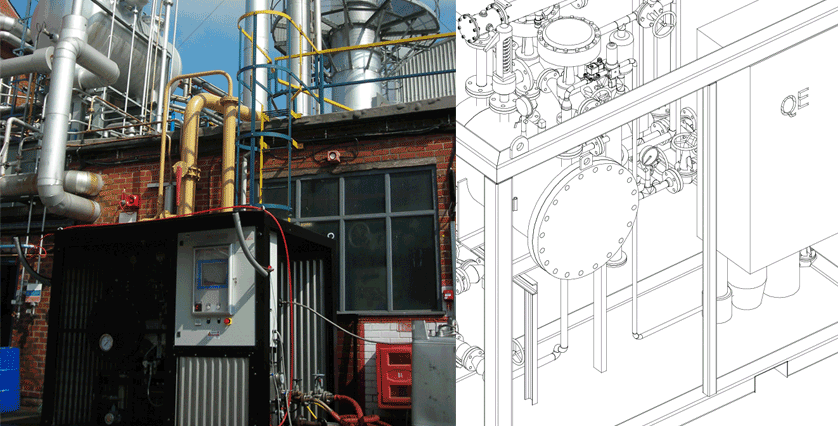
Benefits
- Reduced risk and improved safety
- Guaranteed flash and fire points
- No system downtime
- Extended fluid life
- Reduced waste
- Consistent heat transfer performance
- Consistent viscosity and vapour pressure
- Reduced carbon footprint
Challenge
Many process industries use thermal oil to transfer heat around the process plant. However, these oils degrade over time due to factors such as high temperatures, high film temperatures and oxidation, causing loss of thermal efficiency, increased flammability, cavitation, mechanical failure, system downtime and associated costs.
More importantly, when combined with other system conditions, plant safety can be drastically compromised – and it is now a legal requirement to maintain minimum flashpoints.
For many companies the traditional solution to the degradation problem is to periodically replace thermal oil. The sampling and analysis of the fluid is a requirement within the Dangerous Substances and Explosive Atmospheres Regulations (DSEAR is the UK implementation of the EU ATEX Directive) and the fluid must be conditioned or changed when the fluid falls out of specification. Similar regulations apply in other EU countries. Unfortunately, this reactive process requires the expense of replacing huge amounts of oil resulting in long periods of downtime whilst the system is drained and then re-filled.
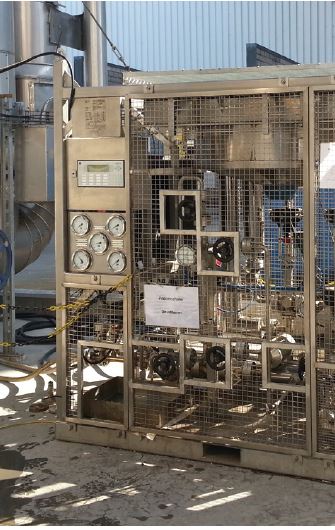
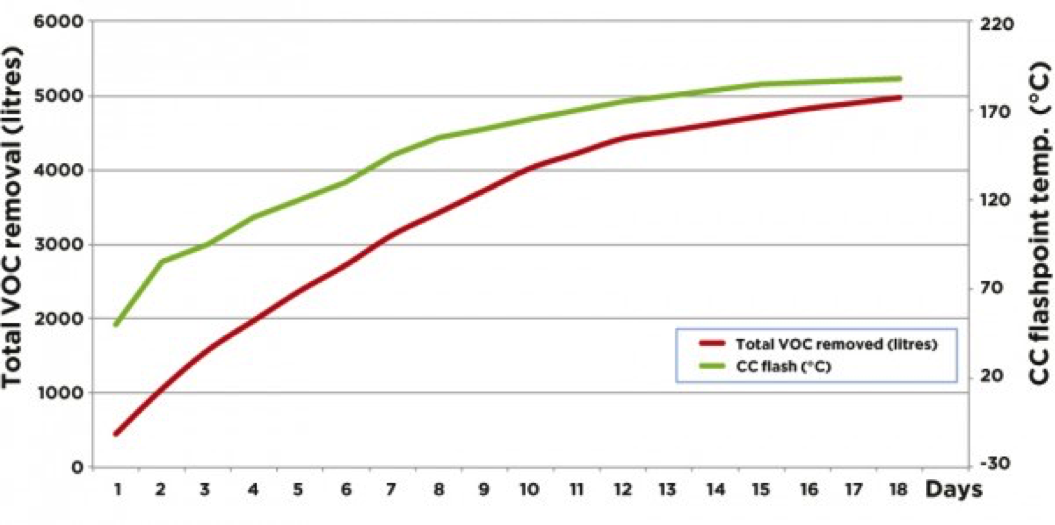
(Data from a 100,000L mineral oil system).
Flashpoint Testing
In our purpose built laboratory, we use two main tests to assess the flashpoint of thermal oil:
Pensky-Martens closed cup flash test: involves heating a sample through a prescribed temperature increase under a closed housing. When the target temperature is reached, a source of ignition is intermittently inserted until the vapour ignites and flashes.
Test conditions replicate enclosed spaces in industrial settings such as ovens, air heat exchangers or leaks into insulation.
Cleveland open cup flash test: follows the same format as the closed cup test but the sample is heated in open air through a prescribed temperature increase with the source of ignition applied every 2°C raise.
Test conditions replicate open air scenarios in an industrial setting like leaks from flanges or pumps, leaks into insulation or exhaust points on ventilation systems.
Quality in Design & Build
TFS has joined forces with Endress+Hauser to develop, manufacture and supply the HT FluidFit flashpoint recovery rigs. With over 60 years of process automation experience, Endress+Hauser has the knowledge and industry experience to provide quality engineering solutions backed by an excellent maintenance and support network across the globe.
If you would like to benefit from our HT FluidFit Service, call our expert team on +44 (0)1298 815862